Products
STA Composites sells a wide range of stock products, including ready-to-use plate, tube, and sheet composite materials. We also offer composite reinforcement fabrics, epoxy resins, vacuum bagging systems and composite fabrication supplies.
As a manufacturer, STA Composites can deliver high quality composites from prototype to production by offering a complete range of services from design, to prototyping, to production of composites. Primary focus is on developing and manufacturing products for the automotive, aerospace and defense industries.
Carbon Fiber
Carbon fiber offers technical properties that are popular in various applications where its high strength-to-weight ratio is of importance. In addition to its high strength-to-weight ratio, carbon fibers are thermally and electrically conductive. They have high tensile strength, low density, low weight, low thermal expansion and excellent fatigue resistance.
STAC’s carbon fiber products are manufactured with PAN based medium modulus carbon fiber, not graphite. Carbon fiber has the highest specific stiffness of any commercially available fiber and a very high strength in both tension and compression. The carbon fibers have a surface treatment applied to improve matrix bonding and a chemical sizing which serves to protect the fibers during handling. To maximize the fiber properties, we recommend using an epoxy based resin.
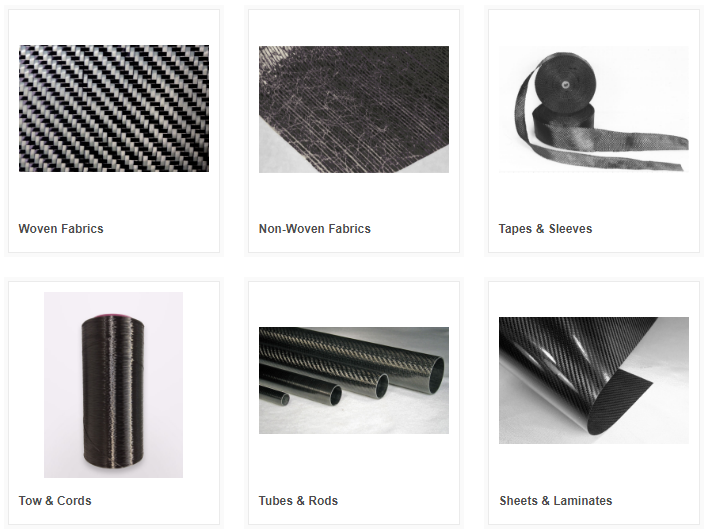
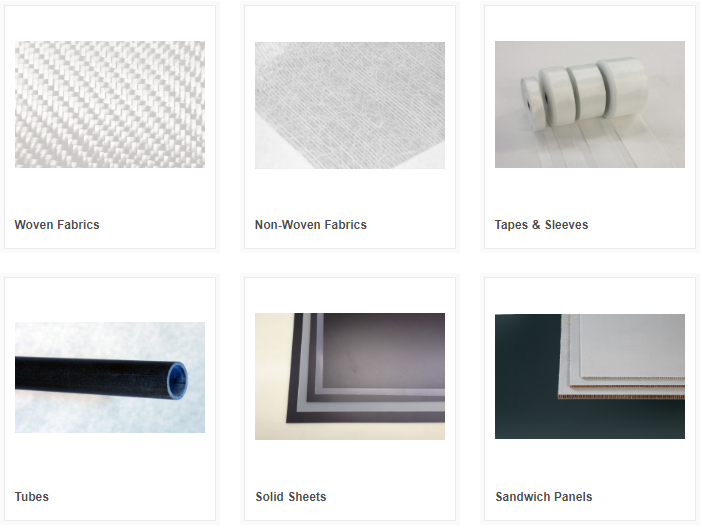
Fiberglass
Fiberglass fabric is used in a wide range of industrial applications and is the most widely available and least expensive composite fabric. It is relatively lightweight, has moderate tensile and compressive strength and is easy to handle and machine. High strength, dimensional stability, design flexibility and excellent electrical properties are some of the characteristics that insure optimum performance.
There are several types of glass fibers manufactured but only two are widely used in composites: E-glass and S-glass. The most common is E-Glass or Electrical Glass. E-Glass is made from strands of continuous glass filaments that are plied and twisted into yarns and is used when strength and high electrical resistivity is required. S-Glass or Structural glass is approximately 30% stronger and stiffer than E-Glass and offers better properties at elevated temperatures.
All fiberglass fabrics offered are sized with an epoxy and polyester compatible finish to enhance wet-out, unless otherwise noted.
Aramid
Aramid (Kevlar®) fibers were first developed by DuPont® in the early 1970’s. These fibers are an organic fiber found in the aromatic polyamide (aramid) family and are typically gold in color.
Aramid is best suited for applications where toughness is preferred. In addition, Aramid fibers offer high strength, low weight, desired stiffness and thermal stability. These fibers are 43% lighter than fiberglass, twice as strong as E-glass, and ten times as strong as aluminum. These unique properties make it an exceptional fiber for use in composite reinforcements, ballistics applications, ropes, cables and protective apparel.
Due to these unique properties we recommend using specialized shears for cutting. Aramid fiber is difficult to sand and is adversely affected by UV light, so it is often buried under fiberglass or other material.

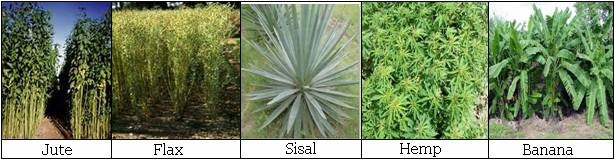
Natural fibers
Natural fibres are defined as substances produced by plants and animals that can be spun into filament, thread or rope and further be woven, knitted, matted or bound. The most viable structural fibres typically derive from specifically grown textile plants and fruit trees.
Nowadays, natural fibres are more up-to-date than they have ever been, as they show outstanding mechanical properties and are 100% sustainable. Flax, jute and balsa are the natural fibres we chose as basic materials for our supreme products. Natural fibre composites with significant reduction in weight became a serious alternative to conventional composite materials like glass and carbon fibres. We are offering all kind of natural fibers.
Surface veil
Surface veil is a lightweight, advanced, non-woven fiberglass veil incorporating 100% E-Glass fibers, approximately 1″ in length, bonded together in a random fiber matrix. The non-woven construction allows a resin-rich surface that increases chemical stability and reduces the risk of micro-cracks forming in the composite surface. It has excellent formability and drape and wets out evenly.
Surface veil can be used to provide a smooth covering for composite structures or to add stiffness with minimal weight gain and thickness. It is compatible with polyester, vinyl-ester and epoxy resins and is suitable for use in wet layup, vacuum bagging and resin infusion manufacturing.

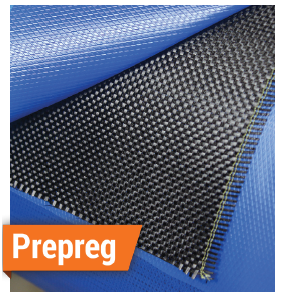
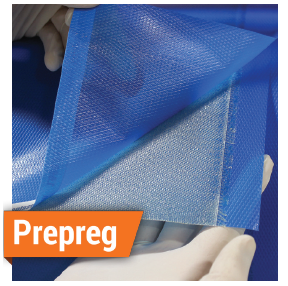
Prepregs
Prepreg is a term used for a composite material that has been “pre-impregnated” with a resin system. Most commonly used prepregs are impregnated with thermosetting epoxy resin and remain tacky until cured. Prepregs often require cold storage and a combination of pressure and heat to fully cure. In general, prepregs are environmentally cleaner, use less toxic materials and produce less outgassing and fumes than those products used during the wet layup process.
Vacuum Bagging materials
Vacuum bagging is widely used in the composites industry. It is a technique in which you create uniform pressure to the surfaces of the object inside of a bag, holding parts together while the adhesive cures. Pressurizing a composite lamination serves several functions. It removes any trapped air between layers and provides pressure that prevents shifting of fiber orientation during cure. It also reduces humidity and improves the fiber-to-resin ratio in the composite part.

Resin, Adhesives & Additives
Core materials
